İklimlendirme (Heating, Ventilating & Air Conditioning) sistemlerinin otomasyonu, Türkiye’de bina otomasyonu deyince akla gelen ilk kalemdir. Özellikle Klima Santralleri (Air Handling Unit) ile merkezi ısıtma ve soğutma sistemlerinin düzgün, efektif ve verimli çalışması için otomatik çalışma özelliği bir zorunluluk haline gelmiştir. Farklı cihazların (pompa, vana, fan, damper gibi) senaryo kapsamında sıralı ve otomatik çalışabilmesi için akıllı kontrol şarttır. Otomasyon kapsamında havalandırma ile ısıtma-soğutma cihazlarının kontrolü sağlanırken, yangın ve kullanım suyu tesisatları ile pis su cihazlarının da izleme işleri yapılmaktadır. İklimlendirme kontrolü konfor ve tasarruf amaçlı olduğu kadar, temiz oda, laboratuvar, ilaç, gıda ve lojistik sanayi gibi alanlarda hem üretim hem de depolama kalitesi açısından bir zorunluluk halini almıştır.
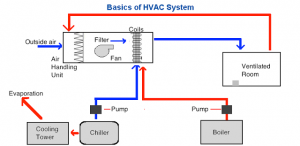
İklimlendirme otomasyonu sadece iklimlendirme cihazlarını değil, kontrol veya izlemeye uygun diğer cihazları da kapsayabilir. Örneğin temiz su, pis su, arıtma veya yangın tesisatındaki cihazların izlenmesi veya jeneratörden bilgi alınması gibi. Ancak asıl kontrol, kazanlar, boylerler, soğutma grupları ve kuleleri, pompalar, vanalar, fanlar, damperler ve klima santralleri gibi cihazlar için yapılmaktadır. İklimlendirmeyi temel olarak 4 gruba ayırabiliriz; merkezi ısıtma, merkezi soğutma, havalandırma ve oda kontrolü.
İKLİMLENDİRME CİHAZLARI
Yukarıda verdiğimiz sırayla gidersek, merkezi ısıtmanın başrol oyuncusu elbette ki kazanlardır. Katı, sıvı veya gaz yakıtlı olması, yoğuşmalı olup olması, büyük kazan yerine kaskatı kombi olması otomasyon açısından büyük bir fark arz etmemektedir. Zaten kazanların kendi brülör kontrolleri ve kumanda panoları mevcuttur, otomasyon cihazın kendi iç çalışma dinamiklerine müdahale etmez. Herhangi bir sorun durumunda kazanın bağımsız çalışabilmesi istenir. Otomasyon kazanları durdurup çalıştırabilir, arıza, sıcaklık ve basınç gibi bilgileri izleyebilir. Giriş çıkış sıcaklıklarına göre şönt pompası veya 3-yollu vana kontrolü yaptırmak da mümkündür ancak günümüzdeki kazan panelleri bu kontrolleri de kendileri yapabilmektedir.
Boyler İngilizce “kazan” anlamındaki “boiler” kelimesinden dilimize geçmiştir, ancak türkiyede boylerin kullanımı sıcak su deposu (akmülasyonu tankı) benzeridir ve kullanım suyunu sıcak tutmak amacıyla kullanılır. Boyler alt girişten kullanım suyu tesisatından soğuk suyu alır ve içerisindeki eşanjörden geçen ısıtma suyu yardımıyla bu suyun ısınması sağlanır. Üst çıkıştan resirkülasyon pompaları yardımıyla sıcak su musluklarına kullanım suyu gönderilir. Musluklar açılıp boylerde bekleyen su tüketildikçe alttan yeni soğuk su alınır ve içeride tekrar ısıtılır. Tankta bekleyen suyun fazla ısınması halinde serpantine giren sıcak su kesilmelidir, aksi halde musluklara aşırı sıcak su gönderilir. Boylerdeki su musluklaa gittiği ve tüketildiği için sirkülasyondaki ısıtma suyu direk verilmez, kullanım suyunun ısıtılmasını sağlar. Güneş enerjisinden faydalanma amacıyla kullanılan çift eşanjörlü boylerlerde güneş enerjisi kısmından gelen su yeterince sıcaksa ısıtma için kullanılır, soğumaya başlaması halinde suyu soğutmaması için girişi kesilir ve kazan/kombi suyuyla ısıtma yapılır. Kim yerlerde elektrikli ısıtıcılı (rezistanslı) boyler de kullanılmaktadır.
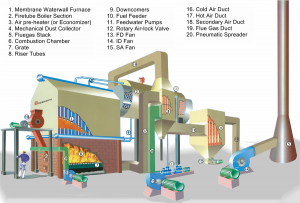
Pompalar sulu sistemlerin kalbidir, tesisatta suyu dolaşmasını sağlama görevi onlara aittir. Bu yüzden hem ısıtma hem soğutma hem de diğer sulu sistemlerde yer alırlar. Hidrofor pompaları hat basıncını ayarlayan, musluklara sürekli basınçlı su gitmesini sağlayan ve bunu kendi kontrol panosu ve sensörü ile yapan pompalardır. Yangın pompaları da yangın söndürme tesisatında basınçlı su kalmasını sağlamakla görevlidir, ayrıca yangında çalışmaya uygun olması gereklidir. Bu tip pompaların otomasyondan sadece izlemesi yapılır. Ancak sirkülasyon ve resirkülasyon pompalarının kontrolü çoğunlukla otomasyona aittir. Pompaların çalışması kritik olduğundan her zaman asıl+yedek mantığıyla tasarlanırlar, çalışan pompa arızaya geçtiğinde yedeğin devreye girmesi çok önemlidir. Ayrıca yedekli pek çok sistemde olduğu gibi, cihazların ömrünü uzatmak için eşyaşlandırma yapılır. Sürekli tek bir cihazı “asıl” belirleyip ona yüklenmek yerine periyodik olarak (günlük, haftalık veya aylık değişimlerle) diğer cihaz “asıl” olma fonksiyonu kazanır, böylece cihazların birinin hızlıca yıpranması yerine tümü eşit şekilde yaşlanmış olur. Pompalar ihtiyaca göre sabit debili veya değişken debili olabilir. Eskiden değişken debili pompalar için harici frekans konverter alınıp MCC panosundan kontrol edilirken, günümüzde pompalar sürücüsü üzerinde akuple veya sürücülü panosuyla birlikte temin edilmektedir. Bu da otomasyondan debi/basınç kontrolü ihtiyacını kaldırmıştır.
Eşanjörler içinde iki ayrı su sistemi barındıran ve sistemler arasında ısı transferi sağlayan ince plakalı yapılardır. Hem ısıtmada hem soğutmada kullanılabilirler. Amaç tıpkı boylerde olduğu gibi iki su sisteminin karışmamasını, ana ısıtma veya soğutma sistemindeki suyun diğer tarafta kullanılmamasını sağlamaktır. Bundaki amaç kimi zaman boylerde olduğu gibi ikinci sistemin açık bir sistem olmasından kaynaklı olabilir, kimi zamansa ısıtma için yüksek derecede su üretilirken ikinci daha düşük derecede sistemde (mesela havuz ısıtmada 45°C civarı) bir sıcaklık gerekmesinden kaynaklı olabilir veya soğutma için tersi durum. Eşanjörlerde ana ısıtma-soğutma suyu birincil (primer) giriş-çıkışta akarken, asıl kullanılacak ve sahaya gönderilecek su ikincil (sekonder) giriş-çıkışı kullanır. Primer tarafta bulunan motorlu vanayla sekonder tarafta istenen giriş-çıkış sıcaklıklarının yakalanması sağlanır.
Chiller (soğutma grubu) evaparatör ve kondenser diye iki kısımdan oluşan, gelen suyu soğutma amacıyla çalışan, hava kaynaklı veya su kaynaklı olabilen cihazlardır. Tıpkı kazanlar gibi, hatta onlardan çok daha kompleks, kontrol üniteleri bulunmaktadır. İçlerinde bulunan kompresörler, fanlar ve diğer cihazlar bu ünite tarafından kontrol edilir. Ana sistemden gelen su chillerin evaparatör kısmına girer, sıkıştırılmış soğutucu gaz suyun sıcaklığını üzerine alarak buharlaşır ve suyun soğumasına sebep olur, soğuyan su (genelde 7°C’lerde seçilir) tekrar sisteme verilir. Kondenser kısımda ise ısınıp buharlaşan freon gazı tekrar sıkıştırılır, bunun için de soğuması lazımdır. Burada oluşan ısıyı havaya veren cihazlar hava kaynaklı, suya veren cihazlar su kaynaklıdır. Su kaynaklı cihazlar daha verimlidir, ancak bu suyun da tekrar soğutulması gerektiği için daha maliyetlidir. Chillerlerin düzgün ve verimli çalışması için gelen suyun debisinin düzgün olması önemlidir. Bu sebeple su akış anahtarı yeterli debide su algılamazsa cihazı çalıştırmaz, çalışıyorsa da durur. Aksi halde chiller arızaya geçer.
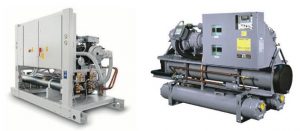
Soğutma kulesi sıcak suyun bir kısmını buharlaştırıp atmosfere atarak soğutan, gerekli sıcaklığa ulaşmış kalan kısmını ise tesise kullanılmak üzere geri gönderen bir cihazdır. Suyun sıcaklığını chiller kadar düşüremez, ancak daha uygun maliyetli bir cihazdır. Bu sebeple su kaynaklı chillerin kondenser bölümünü soğutmada veya WHSP gibi 20-25°C su sıcaklığının yeterli olduğu cihazların souk suyu ihtiyaçlarını karşılamada kullanılır. Altta soğuk su ve ısı tranfer plakaları sayesinde gelen sıcak su soğuyarak aşağı inerken, üstte bulunan fanlarla suyu sıcaklığını atmosfere atılır. Bu ısı transferinin verimini artırmak için bazı kulelerde suyu dolaştırma amaçlı pompalar da yer alır.
Üretilen sıcak su ve soğuk su çoğunlukla ortamı ısıtma-soğutma amacıyla kullanılır, bu ısı tranferini yapmak için de çeşitli cihazlar vardır. Özellikle geniş alanları ısıtıp soğutmak, bir yandan da taze hava sağlamak için en çok kullanılan cihaz Klima Santralidir (AHU). Klima santrallerinde hava alıp işleme ve tekrar içeri verme amaçlı fanlar bulunur, üfleme fanı Vantilatör, emiş fanı Aspiratör olarak geçer. Her santralde alınan havanın temizlenmesi için filtreler, ısıtılması veya soğutulması için de serpantinler bulunur. Ortamı istenen sıcaklığa getirmek veya şartlandırılmış taze hava vermek için üfleme sıcaklığının belli bir derecede olması gerekir. Bunun için de ısıtma veya soğutma serpantinlerinden yeterli ve gerekli miktarda su dolaştırılır, serpantinlerin arasındaki ince plakalardan geçen hava bu sıcaklığı/soğukluğu alır ve içeri üfler. Düzgün bir kontrol için serpantinlerin girişine oransal motorlu vana konulmalıdır, serpantine az su gitmesi havanın istenen dereceye gelmemesine, çok su gitmesi de istenen dereceyi aşmasına yani fazla sıcak veya fazla soğuk olmasına neden olur. Santrallerde ısıtma-soğutma için sulu sistem dışında elektrikli ısıtıcı veya DX batarya kullanmak da mümkündür. DX bataryalar gazlı soğutma (ürün uygunsa ısıtma da) yapar, bunun için VRF dış üniteye ihtiyacı olur. Değişken debili hava kontrolü için EC motorlu fan veya elektrik panosunda Frekans Konverter kullanılır. Üfleme ve emiş kanalına konulacak debi veya basınç (ihtiyaca göre) sensörü ile fanların hızları kontrol edilebilir.
Klima santrallerinde ısıtma-soğutmaya destek amaçlı bazı ısı-geri dönüşüm yöntemleri vardır. Kimi santraller %100 taze havalı iken, aspiratörlü bazı santraller karışım damperli olabilir. Taze hava ve atış ağzındaki damperler kısıp ortadaki karışım damperi açılarak içeriye dışarıdan emilen havadan çok içerideki hava geri verilmiş olur. Böylelikle hali hazırda şartlandırılan havadan faydalanılır. Ancak bu yöntemin fazla kullanılmaz yoğun zamanlarda ortamda taze hava eksikliğine sebep verebilir, bunun için ortamda veya emişte hava kalite sensörü kullanılarak taze hava ihtiyacı kontrol edilmeli, gerektiğinde taze hava damperi oranı artırılmalıdır. Bunun dışında santrallerde reküparatör kullanılabilir, plakalı eşanjörün hava için olanıdır, içeriden gelen havanın sıcaklığının/soğukluğunun bir kısmını ince plakalar yardımıyla dışarıdan alınan havaya aktarır. Isı tekerleği (tambur) ise emişten aldığı havanın bir kısmını üzerindeki süngerli yapıda hapsederek üfleme kısmına taşır, dışarıdaki havaya içerinin şartlandırılmış havasını katmış olur. Ayrıca emişe konan bir serpantinle içerideki sıcaklığı sulu sistemle de üfleme bölümüne taşımak mümkündür.
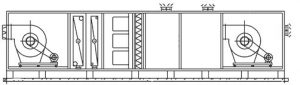
Büyük ortamların ısıtma-soğutması için klima santralleri uygunken, daha ufak ortamlar (ofis odası, otel odası, hastane odası, ameliyathaneler, sistem odaları vs.) için farklı için gerekir. Sulu sistemli yerlerde Fan-Coil Unit (fan ve serpantinden oluşur) veya yerden ısıtma tercih edilebilir. FCU’lar tek fanlıdır, ortamdaki hava emip serpantinle ısıtır veya soğutur, ortama geri verir. Tek serpantinli (2 borulu) cihazlar aynı anda hem ısıtma hem soğutma yapamaz. Bulundukları ortamda yer alan termostattan enerji ve komut alırlar, termostat ihtiyaca göre fan kademelerini ve motorlu vanaları kontrol eder. Yerden ısıtma için de termostat kullanılır, ama fan yoktur, ihtiyaca göre sıcak su vanası açılır kapanır. FCU ve yerden ısıtma taze hava sağlamaz, klima santrali de belli bir derecede hava üfleyebilir. Oda oda şartlandırılmış taze hava için Variable Air Volume (Değişken Hava Debisi) kullanılır. Özünde motorlu dampere benzer, santralden gelen hava odaya girmeden önce VAV’den geçer, ancak VAV geçen havanın debisini okuyarak minimum-maksimum hava debisi kontrolü de yapar. Santralden soğuk hava gelirken içeride soğutma istenmiyorsa debiyi minimuma düşürür, soğutma isteniyorsa maksimum debi sağlayana kadar açar. Tersi durum sıcak hava gelmesi halinde de geçerlidir. Bir odada soğutma yapılırken öbüründe ısıtma yapılabilmesi için genelde üfleme VAV’lerin girişlerine elektrikli (bazen de sulu) ısıtıcı konulur. Düzgün bir kontrol olması için VAV’den sonra sıcaklık sensörü de olmalıdır. Ameliyathane gibi oda-koridor fark basınç kontrolü yapılan yerlerde emiş kanalına da VAV konur, hem sıcaklık hem basınç kontrolü için iki VAV ortak çalışır.
Klima santrali yerine kontrol ünitesi üzerinde olan Rooftop cihazları, oda kontrolü için de gazlı sistem olan WSHP ısı pompaları veya VRF cihazları kullanılabilir. Günümüzde tüm bu cihazların otomasyona uygun haberleşme kart opsiyonları bulunmaktadır. Havalandırma sisteminde ısıtma-soğutmasız taze hava veya egzoz fanları da bulunabilir. Bu fanlar genellikle aç/kapa kontrollüdür, ihtiyaca göre mutfak ve tuvalet egzoz fanları basınç kontrollü olabilir.
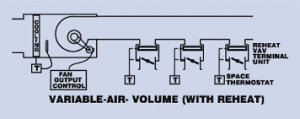
İKLİMLENDİRME OTOMASYONUNDAKİ KRİTİK HUSUSLAR
Mekanik otomasyonunda temel amaç iklimlendirme ve tesisat düşünülerek tasarlanıp konulmuş mekanik cihazlara otomatik çalışma fonksiyonu kazandırmak ve merkezden izleme/kontrol yapılmasını sağlamaktadır. DDC (Direct Digital Control) panolarında bulunan PLC ve I/O modüllerinin girişleri cihazlardaki ve ortamdaki bilgileri okurken çıkışlar de hem kontak hem de oransal olarak kontrolü sağlar. Mekanik cihazların elektrik beslemesinin yapıldığı panolar MCC (Motor Control Circuit) olarak isimlendirilir. Pompa veya fan gibi elektrik motorlu cihazların motorları buradan enerjilendirilir ve kontrol edilir. Sabit debili cihazlarda kontaktörlü düzenek kurulur. Değişken debili cihazlar içinse frekans konverter gerekir, bu bazen MCC panosunun içinde bazen cihazın üzerinde akuple olur. Arıtma cihazı gibi motoru olmayan ama elektrik ihtiyacı duyan veya VRF gibi içinde kendi kumanda düzeneğini barındıran cihazlar için genelde sadece sigorta yeterlidir, bu cihazların otomasyonla bağlantısı kurulacaksa zaten aletin üzerindeki düzenekle kurulur.
MCC panosu mekanik otomasyonda önemli bir noktadır. Özellikle MCC imalatı elektrik taahhüt firmasına bırakılmışsa ve tasarım aşamasında otomasyona yönelik ihtiyaçlar belirtilmemişse panonun otomasyona bağlanması ciddi zorluk doğurabilir. Bunun için otomasyon firmasından MCC’den kontrol edilecek her cihaz tipi için tipik kumanda şeması örneği (MCC-DDC Arayüz) alınmalıdır. Bu arayüzde hem otomasyonun kontrol edeceği ve izleyeceği bilgiler yer almalı, hem de cihazlara özel (AHU’larda donma koruması gibi) kumanda kilitlemeleri belirtilmelidir. Güç ve kumanda çizimi bu şemalar dikkate alınarak yapılmalı, imalattan önce mutlaka onay istenmelidir. Elbette ki MCC panosunun otomasyon firmasına yaptırılması da bir çözümdür, teknik şartnamelere uyulduğu sürece cihazlar sorunsuz çalışır. Hatta bu tip durumlarda zaten birbiri arasında pek çok bilgi alışverişi olacak olan MCC ve DDC panoları, uygun lokasyonlarda tek pano olarak imal edilip hem maliyet avantajı sağlanabilir hem de aradaki kablo çekimi ve bağlantı işçiliğine gerek kalmamış olur.
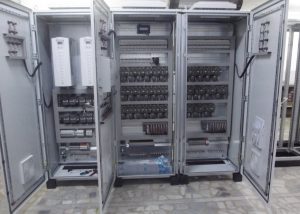
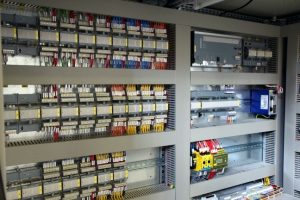
Tabi ki her şey MCC panosunda kontrol edilemez. Sahada otomasyona ait algılayıcılar ve vana veya damper motoru gibi aktüatörler yer alır. Klima santrali ısıtma-soğutma sağlamak için içindeki serpantinle birlikte gelir, ancak üzerinde sıcaklık sensörü veya motorlu vana bulunmaz, bunlar otomasyon için sonradan eklenir. Ayrıca hidrofor veya yangın pompası gibi kendi özel panosu olan cihazlar da mevcuttur, bu cihazların bilgileri de kendi panolarından alınmalıdır. Buradaki asıl zorluk tesisat projesine göre mekanik taahhüt firmasının temin ettiği bir ürünün otomasyona bağlanmasındaki problemlerdir. Sadece izleme yapılacak bir noktada bile cihaz otomasyona bilgi verecek özelliklere sahip olmayabilir, verdiği bilgi otomasyon tasarımında düşünülen tipten farklı olabilir. Bu tür sorunların önüne geçmek için hem otomasyon sisteminde her bilginin nasıl alınacağı açık şekilde belirtilmeli hem de ürünler temin edilmeden önce uygunluğu otomasyon firması tarafından kontrol edilmelidir. Özellikle kontrolünün otomasyon tarafından yapılması beklenen, ancak kendi kontrol kartı olan cihazların otomasyon uyumluluğu çok önemlidir.
Otomasyon sisteminin kurulumu da tasarımı da kritik bir konudur. Ülkemizdeki pek çok uygulamada otomasyon için gereken sinyal kabloları sahadaki elektrik taahhüt firması tarafından çekilmekte ve bağlanmaktadır. Ancak imalatta bu konulara her zaman gereken özen gösterilmemektedir. Öncelikle otomasyonda hemen her kablonun ekranlı (shield) olması gerekir. Kimi yerde kablo tipi 2 x 1 mm2, kimi yerde 4 x 0,75 mm2, kimi yerde ise CAT5 veya CAT6 data kablosu gerekebilir. Sistemin düzgün çalışabilmesi için doğru kablo tipinin kullanılması şarttır. Özellikle günümüzde otomasyon kavramı haberleşme üzerine kurulu olması sebebiyle düzgün haberleşmenin sağlanabilmesi için kablolarının ekranlarının topraklanması elzemdir. Elbette bir de bu kabloların güç tavasından değil, ayrı bir zayıf akım tavasından gitmesi gerekmektedir. Aksi halde ne kadar topraklansa da üzerinde aşırı akım çeken bir güç kablosu olan sinyal kablosunda bozulma önlenemez. DDC panolarının UPS (kesintisiz güç kaynağı) ile beslenmesi de çok önemli bir durumdur. Hem enerji gitse bile bunu görüp hasar kontrolü ve doğru müdahale adına otomasyon sisteminin ayakta kalması için, hem de panodaki hassas modüllerin enerjideki bozulmalardan etkilenmemeleri için düzgün beslenmeleri gerekir.
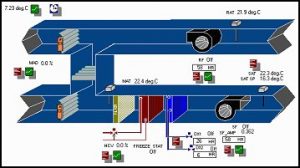
Hem mekanik hem de diğer otomasyon kollarında kritik başka pek çok husus mevcut, ancak kalanlara önümüzdeki yazılarda değineceğiz. Siz de hem sorularınızı hem de yorumlarınızı bizimle paylaşmaktan çekinmeyin. Merak ettiğiniz başka konuları bize iletirseniz, ilerleyen yazılarımızda onlara da yer vermeye çalışırız.